Chemical-resistant valves play a critical role in industrial applications where corrosive fluids are present. These specialized valves are engineered to maintain structural integrity and operational efficiency when exposed to aggressive chemicals, making them indispensable in industries such as lithium processing, chemical manufacturing, and wastewater treatment. Among the various materials available, UPVC (Unplasticized Polyvinyl Chloride) and CPVC (Chlorinated Polyvinyl Chloride) have emerged as leading choices due to their exceptional chemical resistance properties and cost-effectiveness compared to metal alternatives.
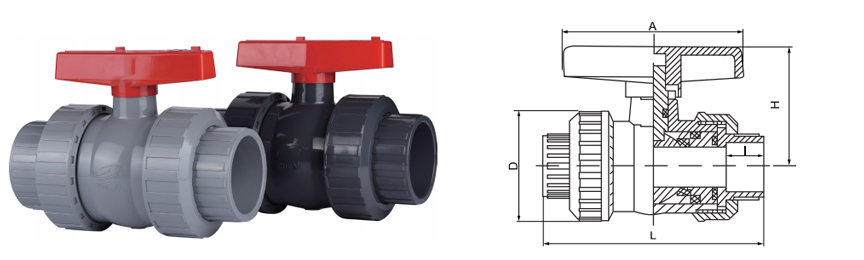
The selection of UPVC or CPVC valves for chemical applications is driven by several compelling advantages that make them superior to traditional metal valves. First and foremost, these thermoplastic materials demonstrate remarkable inertness when exposed to a wide range of corrosive substances, including strong acids, alkalis, and solvents commonly encountered in lithium processing and chemical manufacturing. This non-reactive nature eliminates the risk of galvanic corrosion that plagues metal valves, significantly extending the service life of the entire piping system.
Beyond their chemical resistance, UPVC and CPVC valves offer substantial practical benefits. Their lightweight construction facilitates easier handling and installation compared to heavy metal valves, reducing labor costs and installation time. The smooth interior surfaces of these plastic valves minimize turbulence and pressure drop, enhancing fluid flow efficiency. Additionally, these materials provide excellent dielectric properties, making them ideal for applications where electrical insulation is required. From a maintenance perspective, the non-stick surface of these plastics prevents scaling and buildup, reducing cleaning requirements and downtime.
1.2 Key Differences Between UPVC and CPVC Valves
While UPVC and CPVC share many beneficial properties, understanding their distinct characteristics is crucial for proper valve selection. The fundamental difference lies in their molecular structure - CPVC undergoes an additional chlorination process that enhances its thermal stability and chemical resistance. This modification results in several performance variations that engineers must consider when specifying valves for specific applications.
The temperature tolerance represents one of the most significant differentiators between these materials. Standard UPVC valves typically maintain their structural integrity up to 60°C (140°F), while CPVC valves can reliably operate at temperatures up to 93°C (200°F). This makes CPVC the preferred choice for processes involving hot chemicals or steam applications. In terms of mechanical strength, CPVC generally offers higher pressure ratings and better impact resistance at elevated temperatures compared to UPVC.
Chemical resistance profiles also vary between the two materials. While both resist a wide range of corrosive substances, CPVC demonstrates superior performance with certain chemicals at higher temperatures. For example, CPVC maintains better resistance to concentrated acids and oxidizing agents when operating near its maximum temperature threshold. However, for many standard chemical applications at moderate temperatures, UPVC provides perfectly adequate resistance at a lower cost.
Feature |
UPVC Valve |
CPVC Valve |
Max Temperature |
60°C (140°F) |
93°C (200°F) |
Chemical Resistance |
Excellent for most acids & alkalis at moderate temps |
Superior for hot chemicals and oxidizing agents |
Cost |
More economical |
20-30% higher cost |
Pressure Rating |
150 psi max |
200 psi max |
Installation Ease |
Easier to cut and join |
Requires specialized solvent cements |
UV Resistance |
Poor, requires protection |
Slightly better but still needs protection |
Effective content strategy for industrial components requires targeting specific, high-intent search queries that potential customers use when researching solutions. The following five long-tail keywords represent valuable opportunities to attract qualified traffic while facing relatively low competition:
Best UPVC valves for lithium battery manufacturing - Targets engineers and procurement specialists in the rapidly growing lithium-ion battery industry who need reliable fluid handling solutions for corrosive electrolytes. CPVC chemical valves for high-temperature applications - Addresses the needs of chemical plant operators dealing with hot process streams that exceed UPVC's temperature limits. Difference between UPVC and CPVC valves in chemical industries - Caters to professionals conducting comparative research before making material selection decisions. How to choose the right valve for lithium processing plants - Provides guidance for system designers working with highly reactive lithium compounds and solvents. Chemical-resistant valve maintenance tips for UPVC/CPVC systems - Offers practical advice for maintenance teams looking to extend valve service life in corrosive environments.
These keywords strike an optimal balance between search volume and competition, while directly relating to the information needs of professionals specifying, purchasing, or maintaining chemical-resistant valve systems. By creating content around these terms, we can establish authority in this niche while attracting highly targeted visitors likely to convert into leads or customers.
The lithium battery manufacturing process presents unique challenges for fluid handling systems due to the highly corrosive nature of electrolytes and other chemicals involved. UPVC valves have become a preferred solution in this industry because they combine excellent chemical resistance with cost-effectiveness and ease of installation. The electrolyte solutions used in lithium-ion batteries typically contain lithium salts in organic solvents, which can rapidly degrade incompatible materials.
2.1 Key Features of UPVC Valves in Lithium Processing
UPVC valves designed for lithium battery production must meet several critical performance criteria. The material's inherent resistance to inorganic acids and organic solvents makes it ideal for handling battery electrolytes. Unlike metals that might contaminate sensitive chemical processes, UPVC maintains purity by preventing leaching of metallic ions into the process stream. The valves' smooth interior surfaces prevent particulate buildup that could otherwise lead to quality issues in battery production.
Specialized UPVC valves for lithium applications often incorporate features like diaphragm seals to prevent leakage of volatile organic compounds. Many designs include ESD (electrostatic dissipative) properties to mitigate the risk of sparks in environments handling flammable solvents. Manufacturers may also offer radiation-stabilized UPVC formulations for applications where UV exposure is a concern during storage or handling.
2.2 Common Applications in Lithium Industry
In lithium battery manufacturing plants, UPVC valves serve multiple critical functions throughout the production process. They are extensively used in electrolyte filling systems where precise control of corrosive liquid flow is essential. The slurry mixing process, which combines active materials with solvents and binders, relies on UPVC valves to handle abrasive and corrosive mixtures without contamination.
Waste acid handling systems in battery plants utilize UPVC valves for their resistance to acidic byproducts generated during electrode formation. Cooling systems that regulate temperature during battery formation also employ UPVC components due to their reliability in water/glycol mixtures. Additionally, UPVC valves play important roles in solvent recovery systems, where they withstand exposure to aggressive organic chemicals like NMP (N-Methyl-2-pyrrolidone).
CPVC Chemical Valves for High-Temperature Applications
When chemical processes involve elevated temperatures beyond UPVC's capabilities, CPVC valves provide an excellent alternative that maintains all the benefits of thermoplastic construction while offering enhanced thermal performance. The chlorination process that transforms PVC into CPVC increases the material's glass transition temperature, allowing it to maintain structural integrity under more demanding thermal conditions.
3.1 Advantages of CPVC in High-Temperature Settings
CPVC's superior thermal stability makes it particularly valuable in chemical plants where processes operate at temperatures between 60°C and 93°C - a range where UPVC would soften and fail. This expanded temperature capability comes without sacrificing the material's excellent corrosion resistance. CPVC valves maintain their mechanical strength at these higher temperatures, ensuring reliable operation in pressurized systems.
The material's thermal properties also contribute to reduced energy losses in hot fluid systems compared to metal valves. CPVC's lower thermal conductivity means less heat transfer to the surrounding environment, improving energy efficiency in temperature-controlled processes. Additionally, CPVC's coefficient of thermal expansion is more predictable than many metals, simplifying the design of piping systems subject to temperature fluctuations.
3.2 Where to Use CPVC Valves in Chemical Plants
CPVC valves find numerous applications throughout chemical processing facilities where temperature and corrosion resistance are paramount. They are particularly well-suited for hot acid transfer lines carrying concentrated sulfuric, hydrochloric, or phosphoric acids at elevated temperatures. In chemical synthesis processes, CPVC valves reliably handle reactive intermediates and products at various stages of production.
Steam condensate systems frequently utilize CPVC valves because they resist both the thermal stress of intermittent steam exposure and the corrosive nature of condensed vapors. High-temperature solvent processing, such as in pharmaceutical or specialty chemical production, benefits from CPVC's compatibility with organic compounds at elevated temperatures. The material also performs well in caustic service applications where hot sodium hydroxide solutions are present.
Difference Between UPVC and CPVC Valves in Chemical Industries
Making an informed choice between UPVC and CPVC valves requires a thorough understanding of their comparative performance characteristics across various operational parameters. While both materials share the fundamental advantages of thermoplastic construction, their differences can significantly impact system performance, maintenance requirements, and total cost of ownership.
4.1 Material Composition and Performance
At the molecular level, CPVC contains approximately 30% more chlorine than standard UPVC due to the post-polymerization chlorination process. This additional chlorine content alters the material's properties in several important ways. The increased chlorine atoms hinder the polymer chain's mobility, raising the material's glass transition temperature and improving its heat distortion resistance.
The chlorination process also affects the material's chemical resistance profile. While both materials resist a broad spectrum of corrosive chemicals, CPVC generally shows better performance against certain oxidizing agents and aromatic hydrocarbons at elevated temperatures. However, for many mineral acids and alkalis at moderate temperatures, UPVC provides comparable resistance at a lower material cost.
4.2 Cost vs. Performance Analysis
The decision between UPVC and CPVC often comes down to balancing initial costs against long-term performance requirements. While CPVC valves typically command a 20-30% price premium over comparable UPVC models, this additional investment may be justified by extended service life in demanding applications. The following table provides a detailed comparison of cost versus performance factors:
Factor |
UPVC Valve |
CPVC Valve |
Initial Cost |
$ (Most economical) |
$$ (20-30% higher) |
Lifespan in Corrosive Service |
5-7 years typical |
8-10 years typical |
Maintenance Frequency |
Low |
Moderate (higher temp may affect seals) |
Temperature Limitations |
May require replacement if process temps increase |
Accommodates most process temp increases |
Total Cost of Ownership |
Lower for moderate temp applications |
Better value for high-temp applications |
The choice between materials should consider not just current needs but potential future process changes. CPVC's broader temperature range provides more flexibility if process conditions might change, potentially avoiding costly system retrofits. However, for stable, moderate-temperature applications, UPVC often represents the most cost-effective solution.
How to Choose the Right Valve for Lithium Processing Plants
Selecting the optimal valve solution for lithium processing applications requires careful consideration of multiple technical and operational factors. The highly reactive nature of lithium compounds, combined with the corrosive electrolytes used in battery production, creates a challenging environment that demands specially engineered valve solutions.
5.1 Step-by-Step Selection Guide
Chemical Compatibility Assessment: Compile a complete list of all chemicals the valve will contact, including concentrations and temperature ranges. Consult chemical resistance charts for both UPVC and CPVC to verify compatibility. Pay special attention to organic solvents used in lithium electrolytes. Temperature Profile Evaluation: Determine the maximum and minimum temperatures the valve will experience during normal operation and any cleaning/sterilization cycles. Remember that temperature spikes during process upsets may exceed normal operating ranges. Pressure Requirements Analysis: Calculate both working and potential surge pressures in the system. While both UPVC and CPVC have good pressure ratings, ensure the selected material can handle peak pressures at the highest operating temperature. Flow Characteristics Consideration: Evaluate flow rates, viscosity, and any particulate content in the fluid. Select valve types (ball, diaphragm, butterfly) that provide optimal flow control with minimal pressure drop for your specific application. Regulatory Compliance Verification: Ensure selected valves meet all applicable industry standards and regulations, particularly for lithium battery manufacturing where safety and purity standards are stringent.
5.2 Common Mistakes to Avoid
Several pitfalls frequently undermine valve selection in lithium and chemical processing applications. One critical error is specifying metal valves based solely on pressure/temperature ratings without considering chemical compatibility. Even corrosion-resistant metals like stainless steel can fail rapidly in lithium processing environments.
Another common mistake is overlooking the effects of thermal expansion in plastic valve systems. Unlike metals, thermoplastics expand significantly with temperature increases, requiring proper support and flexible connections to prevent stress buildup. Engineers sometimes underestimate the importance of proper installation techniques for plastic valves, particularly the need for correct solvent welding procedures and adequate cure times for CPVC joints.
Perhaps most importantly, many facilities make the error of selecting valves based solely on initial cost rather than total lifecycle cost. While UPVC valves may appear more economical initially, CPVC might offer better long-term value in applications approaching UPVC's temperature limits where premature failure could occur.
Chemical-Resistant Valve Maintenance Tips for UPVC/CPVC Systems
Proper maintenance practices are essential to maximize the service life and reliability of chemical-resistant valve systems. While UPVC and CPVC valves generally require less maintenance than their metal counterparts, neglecting basic care can lead to premature failures, leaks, or process contamination.
6.1 Routine Inspection Practices
Implementing a comprehensive inspection program can identify potential issues before they cause operational problems. Monthly visual inspections should examine valves for signs of stress cracking, particularly around connection points and actuation mechanisms. Discoloration or surface crazing may indicate chemical attack or UV degradation requiring attention.
Operational testing should verify proper valve function through its full range of motion, checking for any stiffness or binding that could signal material degradation or buildup. Inspect seals and gaskets regularly, as these components often fail before the valve body itself. For critical applications, consider periodic ultrasonic thickness testing to monitor material loss in high-wear areas.
Document all inspections thoroughly, noting any changes from previous conditions. This historical data helps identify developing issues and plan preventive maintenance. Pay special attention to valves in high-temperature service, as thermal cycling can accelerate material fatigue in plastic components.
6.2 Troubleshooting Common Issues
Even with proper maintenance, UPVC and CPVC valve systems may experience certain characteristic issues. Leakage at valve stems or seals often develops over time, typically caused by compression set in elastomeric components. For minor leaks, tightening the packing nut may provide a temporary solution, but seal replacement offers the only permanent fix.
Blockages can occur in valves handling slurries or solutions that may crystallize or polymerize. Regular flushing with compatible solvents helps prevent buildup. For existing blockages, avoid excessive force when operating stuck valves, as this can damage plastic components. Instead, apply gentle heat (for CPVC) or chemical cleaning appropriate for the deposit type.
Stress cracking represents one of the most serious failure modes for plastic valves. This typically originates at points of high mechanical stress and propagates through the material. Prevention involves proper installation to minimize residual stresses and avoiding exposure to incompatible chemicals that can accelerate environmental stress cracking.