Understanding the Importance of Specialized Valves in Chemical Processing
The chemical and lithium industries demand exceptionally durable and corrosion-resistant valve solutions. As these sectors handle aggressive media, standard valves often fail to meet operational requirements. This comprehensive guide explores Chemical/Lithium UPVC/CPVC Valve(DIN/ANSI) solutions, comparing materials, standards, and applications to help professionals make informed decisions.
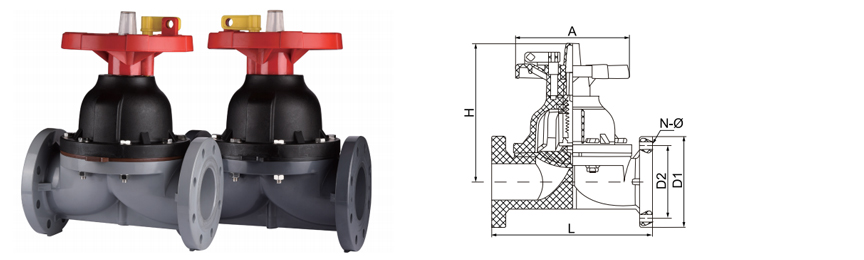
SCH8O/DIN UPVC/CPVC Flang Diaphragm Valve
UPVC valves for lithium battery acid handling: Material Advantages
Why UPVC Stands Out in Lithium Processing
Unplasticized Polyvinyl Chloride (UPVC) valves have become essential components in lithium battery manufacturing facilities. The material's unique properties make it ideal for handling the corrosive acids used in battery production:
- Superior resistance to hydrochloric acid, sulfuric acid, and other electrolytes
- Non-reactive surface prevents contamination of sensitive lithium compounds
- Excellent dimensional stability under thermal stress
- Lightweight construction simplifies installation and maintenance
Temperature and Pressure Limitations
While UPVC offers numerous benefits, understanding its operational limits is crucial for proper application:
Parameter |
UPVC |
CPVC |
Max Continuous Temperature |
60°C (140°F) |
93°C (200°F) |
Pressure Rating at 20°C |
150 psi |
100 psi |
Impact Resistance |
Moderate |
Higher |
CPVC chemical valves DIN standard specifications Explained
DIN Standard Compliance for Chemical Applications
Chlorinated Polyvinyl Chloride (CPVC) valves manufactured to DIN standards provide reliable performance in chemical processing environments. The DIN standard ensures:
- Precise dimensional tolerances for leak-proof connections
- Material quality verification through rigorous testing
- Compatibility with European piping systems
- Standardized pressure ratings for safety
Key DIN Specifications for CPVC Valves
The DIN 8061 and DIN 8062 standards specifically address CPVC piping components, including valves. These standards define:
- Wall thickness requirements based on diameter
- Pressure-temperature relationships
- Quality control measures during manufacturing
- Marking and identification protocols
ANSI rated PVC valves for corrosive chemicals: Performance Comparison
ANSI Classifications and Their Significance
American National Standards Institute (ANSI) ratings provide crucial information about valve pressure capabilities. For corrosive chemical applications, ANSI Class 150 valves are most common, but higher classes may be required for specific processes.
Material Performance Under Chemical Stress
Both UPVC and CPVC demonstrate excellent chemical resistance, but their performance varies depending on the medium:
Chemical |
UPVC Resistance |
CPVC Resistance |
Hydrochloric Acid (20%) |
Excellent |
Excellent |
Sulfuric Acid (50%) |
Good |
Excellent |
Sodium Hydroxide (30%) |
Fair |
Good |
Thermal Stability Advantages
CPVC's superior temperature resistance makes it the preferred choice for many chemical plant applications. The material maintains structural integrity at temperatures where UPVC would begin to soften, offering:
- Extended service life in heated processes
- Reduced risk of deformation under thermal cycling
- Better performance in steam applications
Application-Specific Considerations
Selecting between UPVC and CPVC for high-temperature chemical service requires evaluating several factors:
- Continuous operating temperature requirements
- Thermal expansion characteristics of the system
- Chemical concentration at elevated temperatures
- Pressure fluctuations in the process
Lithium extraction process valve material selection Guide
Special Requirements for Lithium Processing
The lithium extraction process presents unique challenges for valve materials due to the combination of corrosive brines, high temperatures, and abrasive particulates. Key considerations include:
- Resistance to lithium chloride and other salt solutions
- Performance in high-pH environments during purification
- Durability against abrasive slurry flows
Material Comparison for Lithium Applications
While both UPVC and CPVC work well in many lithium processing stages, their suitability varies by specific process step:
Process Stage |
Recommended Material |
Reason |
Brine Extraction |
CPVC |
Better temperature resistance |
Acid Leaching |
UPVC |
Superior acid resistance |
Purification |
CPVC |
Alkali resistance |
Installation and Maintenance Best Practices
Proper Installation Techniques
Correct installation significantly extends valve service life in chemical and lithium applications. Essential practices include:
- Following manufacturer's torque specifications for flange connections
- Using compatible gasket materials for the chemical service
- Allowing for proper thermal expansion in piping systems
- Implementing appropriate support spacing to prevent stress
Maintenance Protocols for Longevity
Regular maintenance ensures optimal performance of Chemical/Lithium UPVC/CPVC Valve(DIN/ANSI) installations:
- Periodic inspection for signs of stress cracking
- Verification of actuator operation in automated systems
- Cleaning of internal components in slurry services
- Replacement of elastomers before failure occurs